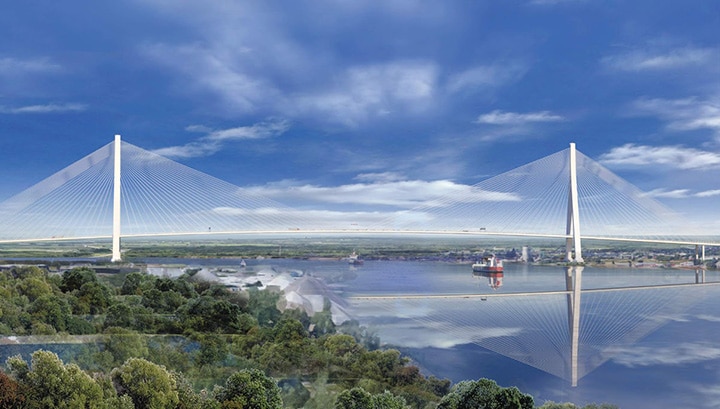
Gordie Howe International Bridge
BOS Environmental Solutions, now Stage 3 Separation, provided slurry management services for the Gordie Howe International Bridge Project representing one of the longest bridges in North America.
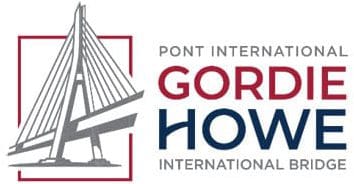
The Mission
Polymer drilling fluid used in the cased drilled shaft process was recycled through the patented BOS tank process for reuse during construction of an international six lane bridge spanning over one and a half miles.
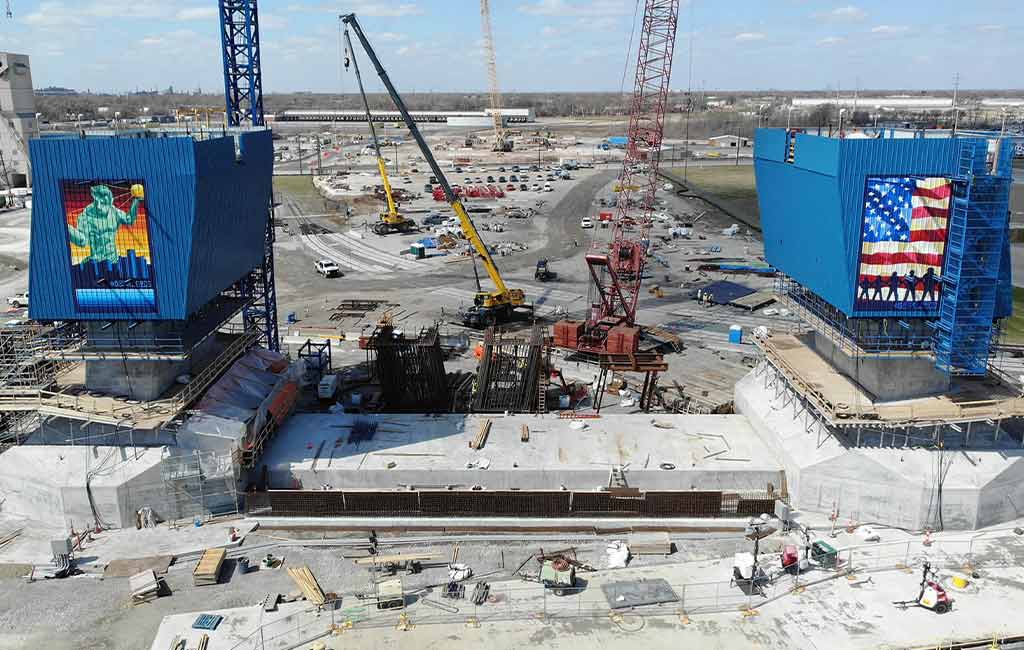
Standard Project Pitfalls
Traditional rental tanks take days for solids to settle out and require significantly more polymer fluid and related surface storage.
This process results in the usage of numerous holding tanks.
More holding tanks result in larger volumes of polymer and increase costs to project.
With a complete fluid management and solids separation process, polymer fluid can be reused throughout duration of project, no hauls-offs, and greater cost savings to customer.
The Objectives
Stage 3 Separation prides itself on providing services that help clients reduce their projects’ carbon fiber footprint. Talk to us about improving your Environmental, Social, and Corporate Governance (ESG) score.
Recycle and reuse polymer drilling fluid throughout project, reducing drilling fluid product consumption.
Reduce project cost associated with polymer fluid disposal, eliminating vac truck haul-off.
Reduce carbon footprint by eliminating unnecessary vac truck disposal loads.
The Solution
The BOS Tank system versatility provided an option for slurry filtration throughout multiple phases of the project.
The primary focus for this job was to use the BOS Tank systems application to process and separate the solids from the polymer, enabling the immediate reuse of fluids throughout the 33 shafts that were completed.
Stage 3 Separation – BOS Environmental Solutions provided the BOS Tank system, two large-bowl centrifuges and a technician who managed the compete fluid system, overseeing the removal of drilled clays, sands, and silts from the polymer fluid. The technician also managed the mixing of polymer, ensuring the ideal solution composition was achieved for the project site.
The Numbers
32 shafts 6-10’ ft. (2-3m) diameter up to 120’ ft. (36m) deep.
Each shaft contained approximately 60,000 gallons (230 m3) of polymer fluid.
Continued reuse of recycled polymer saved approximately 160,000-gallons (600 m3) from being disposed of every 2 weeks.
The Process
- Approximately 10x 18,000 gallon tanks of polymer fluid is built to specification to begin the project.
- As drilling begins, polymer from shafts, was pumped to holing tank, were processing and removing of solids began.
- Stage 3 Separation – BOS Environmental Solutions processed the polymer slurry daily removing the solids and cleaning the polymer fluid so the client could reuse the same polymer fluid for ongoing and concurrent shafts.
- Solids laden polymer fluid returning to surface from drilled shaft is processed through the BOS system, and the clean recovered polymer fluid is then pumped back to shaft for immediate reuse.
- Conventional Fluid Management:
- Settling tanks rely on gravity to settle solids, which can take days for solids to drop out of polymer for reuse. Over time many of the solids become colloidal in size and no longer settle under atmospheric gravity resulting in ever increasing weight of the polymer fluid. Ultimately the fluid becomes unusable, which then must be disposed.
- The conventional process also requires a much larger footprint for holding tanks and requires separate segregated fluid storage. This alone doubles the amount of polymer needed in the operation.
- Conventional Fluid Management:
- The typical operation would require tanks to be cleaned with vac trucks as the solids increased in each tank. There were no vac trucks required for the project, until the end for cleaning the tanks, before leaving site.
- All processed polymer fluid generated a solid, stackable, and paint filter pass waste stream that went directly to clean landfill.
- Our technicians performed proper onsite testing to ensure target fluid rheology was achieved for all reused polymer drilling fluid throughout the process.
The Conclusion
The successful integration of the BOS Filtration System and dedication to on-site fluids management achieved significant reduction in operational costs by reducing drilling fluid consumption and associated disposal fees.
Additionally, recycling and reusing the polymer drilling fluid contributed to time and cost savings which met the fluid management and rheology objectives. This reduction eliminated numerous trucks off public roadways and contributed to an overall positive ESG effort.
For more information about this project or how Stage 3 Separation – BOS Environmental Solutions can service your next project please contact us today.